Investments in Talent Improve Costs
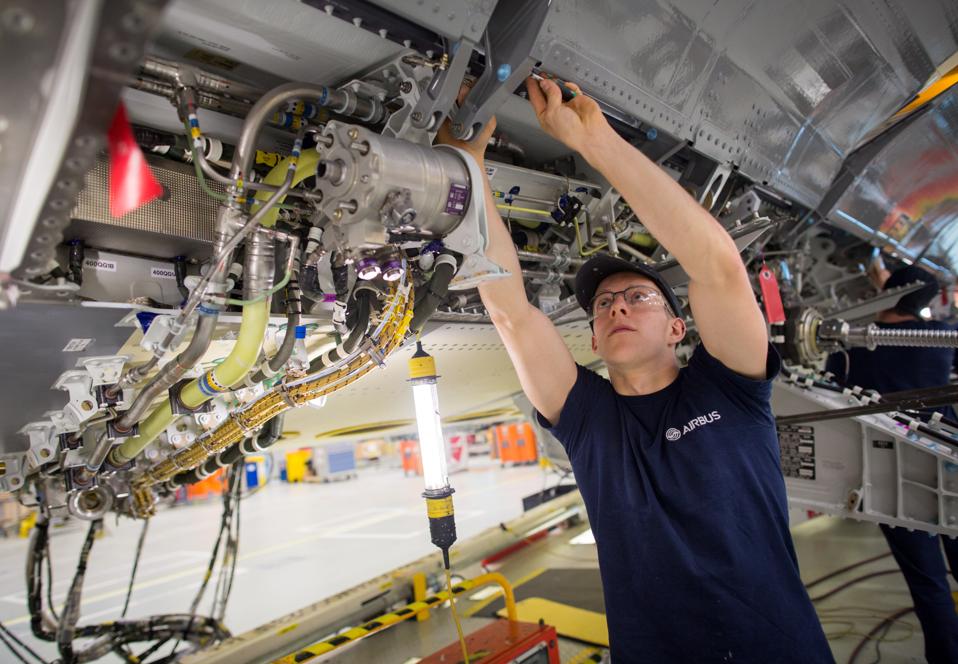
BRISTOL, ENGLAND – NOVEMBER 19: A skilled fitter works on the spoiler of a A400M at the Airbus aircraft manufacturer’s Filton site on November 19, 2015 in Bristol, England. The site at Filton’s main role is the designing and manufacture of wings, fuel and landing gear systems for all ranges of Airbus aircraft currently employing over 4,000 people. It is estimated another 100,000 jobs are generated in the UK by Airbus wing work, both directly as well as indirectly through an extended supply chain of over 400 companies. (Photo by Matt Cardy/Getty Images)
Supply chain processes are relatively new. The processes are evolving. While the practices of finance are over 200 years, in contrast, supply chain as a cross-functional practice (the combination of make, source and deliver) was only defined in 1982. In a recent study, our goal was to understand the impact of process and technology choices on balance sheet performance. We analyzed the impact of 150 factors on 493 financial metrics for the period of 2004-2016. This included responses to 3604 questions by 1063 individual respondents in 40 studies representing 756 unique companies.
This was tough work. It took us four months. The results? There is no correlation between technology choices and balance sheet results. Despite all the ads at airports and pretty powerpoints by consultants, we cannot find support for the claims of “Best Run Companies Use Technology X” or “Manufacturing Companies Using Consulting Services With Company Y Have Better Results.” …or a single instance of Enterprise Resource Planning (ERP) drives better results. Across the industry, we find that companies think that they are managing costs and inventory better through technology investments, but they are not. Through graphing the financial metrics, we find that 90% of companies are stuck at the intersection of operating margin and inventory turns. With rising complexity, they are unable to make improvements in a balanced scorecard.
What made a difference? The answer is simple. Empowered talent. As shown in Figure 1, we find companies managing talent better than their peer group have a significant advantage in managing costs.
Figure 1. Results of Correlations

Correlations to Balance Sheet Results
So what are the characteristics of companies managing talent better than their peer group? What are the gaps to close? There are six: belief in the company, appreciation for work, the need to be a part of a talented team, admiration for leadership, training and professional development and flexible work schedules. Empowered workers make a difference. With the flurry of M&A, industry consolidation, outsourcing, and downsizing, the gaps for North American manufacturers are increasing.
Figure 2. Talent Gaps

Talent Gaps
Overall, 69% of supply chain professionals are satisfied. Baby boomers are happier than Gen X or Millennials. Employees working for technology providers or academics are more satisfied that employees working for manufacturers. This is a warning for manufacturing companies. The gap is significant.
More insular companies–those that do not encourage networking, training, professional experiences–tend to score lower on employee satisfaction. So, if you are working on improving the satisfaction of supply chain employees, consider the elements on the word cloud from the survey open-end responses.
Figure 3. Word Cloud of Open-End Responses

Word Cloud of Open End Responses
Most companies have an endless cycle of cost cutting. The cost cutting is more severe in the back office than the front office teams of sales and marketing. Companies are often so busy pinching pennies that they miss the greater opportunity. With slowing growth, as companies end the year, many teams face draconian cost-cutting efforts. When faced with these choices, just remember that empowered employees drive a competitive advantage. Our take? Talent matters.
No comments:
Post a Comment